With the assistance of Finite Element Analysis (FEA) software specifically designed for elastomeric evaluation, our applications engineers can predict a seal’s performance in a variety of media, temperatures, and pressures. This, in combination with a thorough application analysis, ensures the correct material and size are selected for your particular application needs. For leak troubleshooting assistance, contact us today at: Tulsa: 1 (888) SEALTUL; OKC: 1 (888) OKCSEAL; Houston: (833) TX5-SEAL.
Success Story
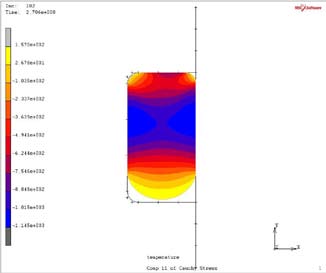
Application:
An automotive customer was proposing an O-ring in a new face seal design, with the temperature ranging from -40°C to 125°C.
Concerns/Problem:
For the proposed design, the customer requested that the following criteria be evaluated through Finite Element Analysis (FEA):
- The minimum pressure exerted against the sealing surfaces by the compressed O-ring.
- The minimum length of contact between the O-ring and the sealing surfaces.
- The maximum principal strain exerted on the compressed O-ring.
- The maximum expected gland fill at the maximum operating temperature.
Parker’s Analysis:
Parker Applications Engineering created a model of the existing face seal in the maximum fill condition. Using FEA software, Parker ran a simulation of the O-ring expansion to determine the degree of overfill at maximum temperature.Based on the results from the original FEA, Parker increased the width of the face seal gland to accommodate the thermal expansion of the O-ring. Parker also analyzed the minimum sealing pressure, the minimum contact length, and maximum principal strain, and they were all found to be within the customer’s specification limits.
Outcome:
Parker Applications Engineering presented the FEA results for both the original and the new design, and the customer redesigned the face seal gland to accommodate the O-ring expansion.
Download this issue of Problem Solved! provided by Parker.
Problem Solved! Is a publication of Parker Hannifin Corporation.