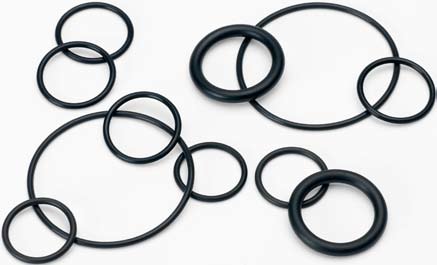
In any type of application, there are consistent requirements to target when designing an adequate O-ring seal. Compression of the O-ring, gland fill of the O-ring within the gland, and stretch around the piston are critical considerations. A more detailed description of these requirements follows:
Squeeze: The amount that the “free state” cross-sectional diameter of the O-ring is compressed in the gland. The recommended range depends on the type of application and the cross-sectional width of the O-ring. The minimum amount of deflection for all O-ring seals is 0.007 inches, regardless of the cross-sectional thickness.
Gland fill: The percentage of the gland volume that is filled by the compressed O-ring. Between 70% and 95% gland fill is considered ideal. Excessive gland fill can cause sealing problems as well as contribute to early onset of permanent O-ring deformation.
Inner diameter (ID) stretch: For face seals, no ID stretch is required. For piston and bore type assemblies, ID stretch in the range of 0-5 % is recommended.
In the situation of a high tolerance stack-up in an O-ring sealing design, it is important to consider what the squeeze, gland fill, and ID stretch are at the extreme ends of the tolerance ranges. The goal is to ensure that these parameters are within the recommended range even in the worst case scenario. For leak troubleshooting assistance, contact us today at: Tulsa: 1 (888) SEALTUL; OKC: 1 (888) OKCSEAL; Houston: (833) TX5-SEAL.
Success Story
Application:
Water pump assembly
Problem:
The customer was attempting to seal a joint that was subjected to a highly variable dimensional range due to
a large tolerance stack-up. Due to limited space availability, a slim axial profile for the O-ring was required. Unfortunately, the high tolerances would have an even greater nega- tive affect on a small cross-sectional area. The customer preferred to use an O-ring, but was doubtful that an adequate seal could be maintained.
Parker Solution:
Parker analyzed the sealing con- ditions and experimented with a number of standard O-ring sizes to see what values of stretch, squeeze, and gland fill could be obtained
in both the nominal and extreme dimensional conditions. Using an iterative process, it was determined that a 5-xxx size would best meet the requirements. The largest possible standard O-ring width was chosen to help offset the effects of the high tolerance stack-up.
Outcome:
Using the recommended O-ring, the prototype successfully passed the first round of testing with no leakage. The customer was very satisfied with both the performance of the O-ring in the irregular joint and the avoid- ance of less cost-effective sealing options.
Problem Solved! Is a publication of Parker Hannifin Corporation.