Hydrogen production lies at the heart of the global transition to sustainable energy. Whether through electrolysis, which splits water into hydrogen and oxygen using renewable energy, or steam methane reforming (SMR), a widely used method involving natural gas, the production process must be both efficient and safe to support hydrogen’s growing role in the energy economy.
However, the extreme conditions present in hydrogen production systems create unique challenges—especially when it comes to sealing. Choosing the right seals is critical to ensuring the reliability and safety of these systems.
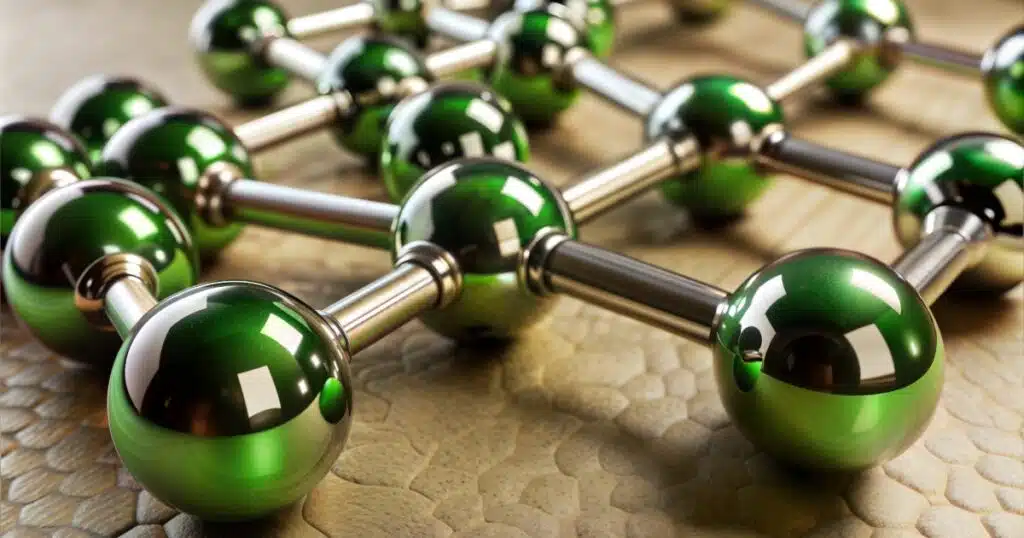
Challenges in Hydrogen Production Systems
- High Pressure: Hydrogen production systems often operate under extreme pressures, exceeding 100 bar in many applications. This environment demands seals that can maintain integrity without compromising performance.
- Corrosive Chemicals: Exposure to steam, methane, and catalysts during production requires seals with excellent chemical resistance to prevent degradation over time.
- Temperature Extremes: Production processes can involve rapid temperature swings, from cryogenic conditions in certain setups to high heat during steam reforming. Seals must remain reliable under these harsh thermal variations.
Innovative Sealing Solutions
At Seal Company, we collaborate with industry leaders like Freudenberg Sealing Technologies and Parker to provide advanced sealing solutions tailored for hydrogen production systems.
Freudenberg Sealing Technologies offers:
- High-performance elastomers: Designed for chemical resistance and durability in high-pressure environments.
- PTFE seals: Exceptional resistance to hydrogen permeation and capability to handle extreme temperatures.
- Compression packings: Engineered for both rotating and static equipment to ensure long-term reliability.
Parker delivers:
- Engineered sealing materials: Resistant to aggressive chemicals and high temperatures, ensuring longevity and performance.
- High-quality O-rings and seals: Tailored for hydrogen production applications where reliability is critical.
Why Seal Company?
At Seal Company, we do more than supply seals—we work alongside your team to understand your specific challenges and recommend the best solution for your application. With access to Freudenberg’s and Parker’s extensive portfolios, we ensure you get a solution tailored to your needs, whether it’s for electrolyzers, reformers, or other critical components.
Our sales staff and engineers are equipped to evaluate your system and recommend the best combination of materials, designs, and technologies to optimize performance and safety.